Want to Chat?
Our team members are happy to answer all your questions.
1300 083 532
sales@freshtrack.com
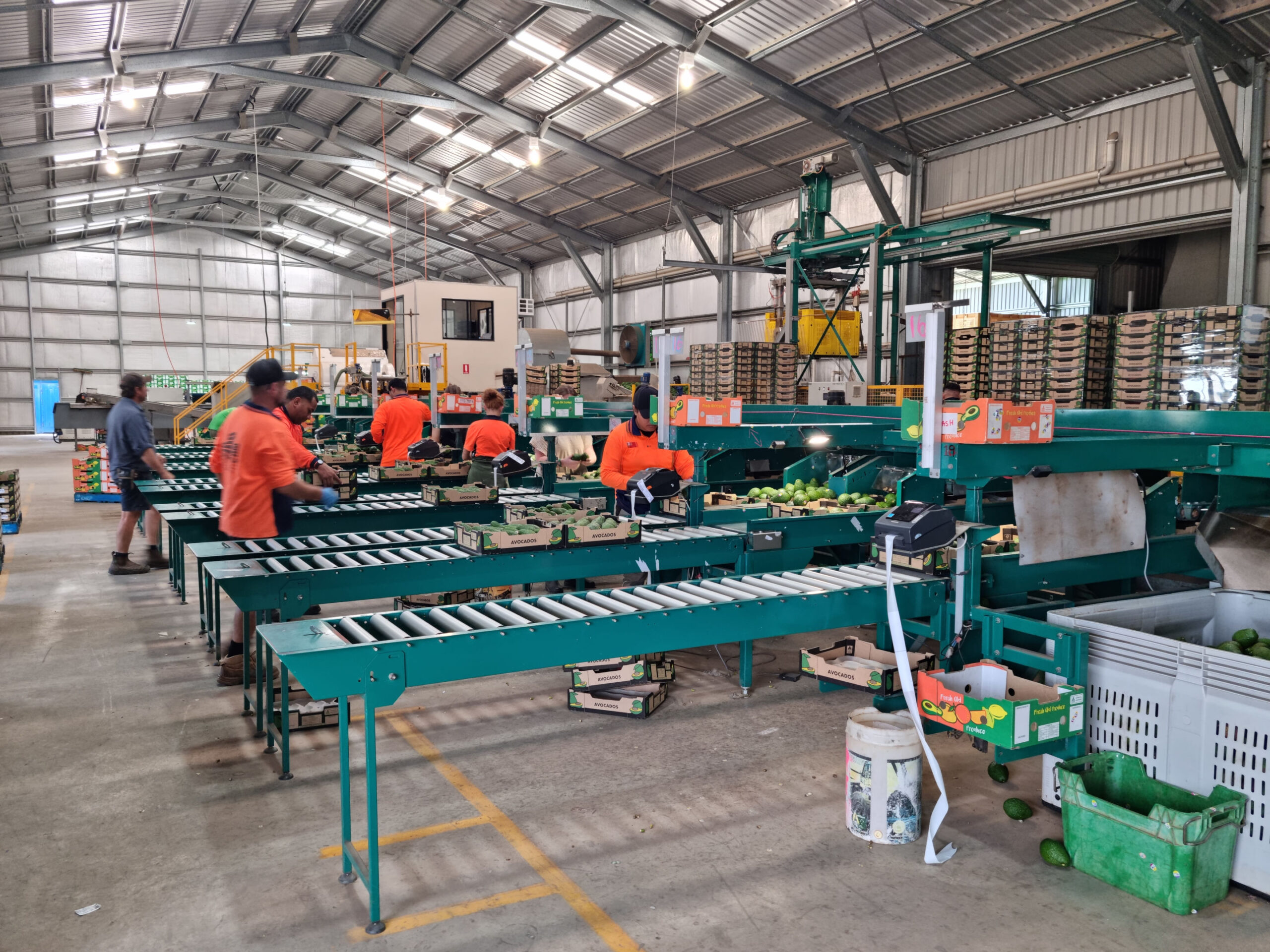
Welcome to the world of modern packing house management with FreshTrack Cloud Packing System. Our innovative solution, Freshtrack Packer System, is here to redefine how you handle fresh produce from field receivals to market. With a focus on practicality and efficiency, The Packer System sets new industry standards for optimizing the packing process.
Freshtrack Cloud Packer System is all about saving you money and time. It simplifies operations and cuts costs at every step of the packing journey. As soon as fresh produce arrives, important batch information is electronically captured and tracked, ensuring complete traceability throughout the process. This data seamlessly flows into storage, guides the grading process, and gets printed on packaging, pallets, and load manifests.
Say goodbye to inefficiencies and embrace a more profitable future with FreshTrack Cloud Packing System’s.
Join the growing community of packing houses that are choosing this game-changing solution to improve their operations and stay competitive. Discover how it can make your packing process smoother, cost-effective, and traceable. Your success is just a click away with FreshTrack Cloud Packing System!
FreshTrack Cloud Packing System, is a cutting-edge traceability and supply chain management solution revolutionizing modern packing houses. With its innovative features and seamless functionality, it sets the gold standard for optimizing the process of receiving, grading, packing, tracing, and consigning fresh produce to market.
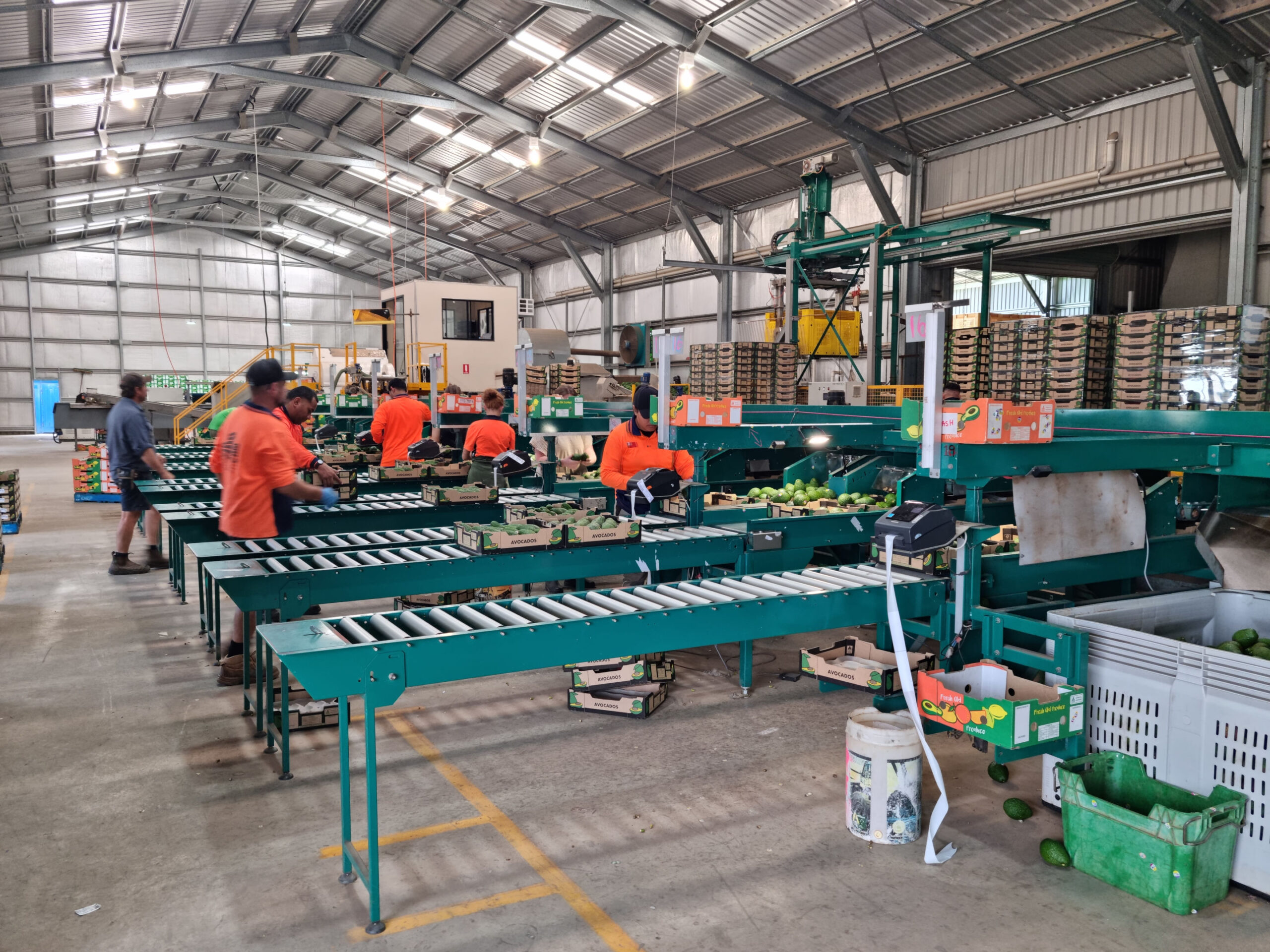
Our Benefits
Packers benefit from key features including real-time reporting, full traceability, monitoring and control, labeling, and automation options. These features streamline operations, increase efficiency, and ultimately benefit you by reducing costs and enhancing productivity.
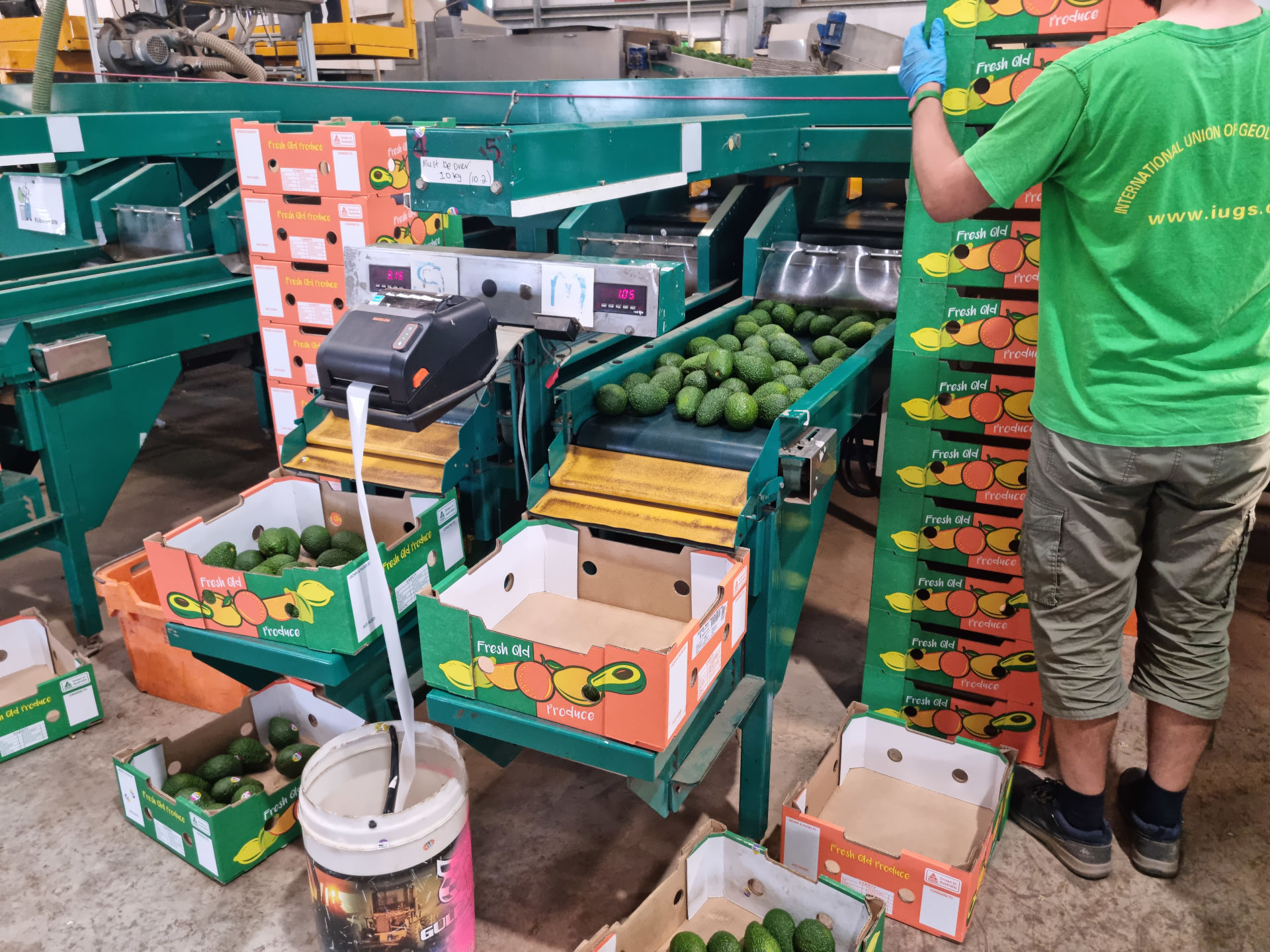
Automated reporting & report delivery.
Detailed chemical & fertilizer usage history.
Full traceability back to the picker.
Improved efficiency through automation.
Point-of-packing labeling.
Handle multiple re-consignments.
Interfaces with Accounting/Payroll systems.
…and much more!
Base Packer System
The Base Receival Module enables you to record harvest deliveries via the web app.
The Base Packing Module allows you to create and label Cartons and Pallets, without requiring the use of a scanner.
The Base Dispatch Module allows you to create consignments and assign pallets via the web app, then print and/or email Consignment and Invoice documents.
Packer System Add Ons
The Asset Maintenance Addon allows you to record service history either by kilometer, hour, or time period. It allows service documents to be stored for easy retrieval, record parts suppliers, service companies, repair history and breakdown history. Assets may be anything that requires regular servicing, e.g. Tractor, Truck, Irrigation Pump, Grader load cells, etc.
The Forecasting Addon allows you to program future order commitments and production supply commitments strategically or tactically. The surplus or deficit from forecasting allows real-time alerts for over or under supply and predicts harvest date, quality and tonnage for committed and actual orders.
The Bill of Materials (BOM) Addon enables product resource management whereby one product may consist of multiple consumable items. They can be part of reports and are directly integrated into the inventory.
With our Industry Standard Inventory System Addon, it is easy to manage purchases, stock takes, draw down from production data, and calculations of re-order points of resource items. When used in conjunction with a Bill of Material, it can draw down multiple inventory items (e.g. when one Count 18 Mango Tray is produced, it can draw down 1 Base, 1 Lid, 1 Liner, 1 Tray Sticker and 18 Fruit Stickers).
The Forms (QA) Addon is used to record virtually anything. It is a user definable template system that replaces all manual record keeping such as forecast yield estimates, harvest produce quality assessments, scales calibrations, packed produce assessments, etc. Assigned to control points, Forms can be referenced from reporting: Grower, Farm, Block, Planting, Harvest Receivals, Bins, Batches, Packed Products, Pallets, Assets, Employees, and more. Templates may prompt users for Photos, Barcodes, RFID Tags, GIS Location, free text, drop-down lists and numeric fields. When Bin/Carton Barcodes or a RFID Tags are read, known information does not need to be re-entered: simply scan a tray barcode and then record presentation and weight. Forms can be performed on workstations or on Android/iOS mobile devices using the FieldOp App.
The Timesheet Addon is used to clock employees in and out from work areas and roles, accurately measuring their work time.
For the Harvest Receival Addon, there are various operational modes for managing bins, including the use of bin tags that are printed and applied upon receipt, permanent bin barcodes or RFID tags, read/write RFID tags, pre-printed bin tags applied in the field, and custom receival systems.
With the Auto Batch Change (ABS) Addon, when a new Batch is detected at the tipper, a batch change sequence is initiated, and point-of-packing label formats change to the new batch as the produce reaches each grader outlet.
The Point-of-Packing Labeling Addon combines batch, outlet, and packer information to be printed. Features include Push Button Labeling, Wristband Reader Labeling, Touch Screen Labeling, Punnet Packing System, Bulk Weighing & Labeling, and a Packing Instruction Screen.
The Packing Line Integration Addon provides integration with packing line automation systems:
- Grader Interface Option: Integration with Grading Line Controllers, allowing changes to only be made once in one system.
- Fruit Stickering Machine Integration Option: Labels printed by FreshTrack's Point-of-Packing systems can include barcodes to control the sticker head position to align to tray counts.
- Inner Product Labelling Option: GS1-13, best-before date, production date/time, current batch number, and more information can be controlled and printed.
- Check Weigher Integration Option: Provides integration with inline check weighers and records actual weight for each carton. Minimum/maximum limits can be set to control whether a carton gets rejected.
The B2B Addon supports integration with Coles, Woolworths, Aldi, and non-EDI buyers through Xchange VAN Service, FreshTrack Xchange VAN Interface, and FreshTrack 3rd Party VAN Interface. Orders can also be imported manually by uploading XML files or CSV spreadsheets.
Contact us for a full list of features and to discuss and explore how we can help you scale your business optimally.